Material Testing For Energy Solutions
ACE LaboratoriesACE offers physical and analytical testing services on rubber, plastic, elastomer and silicone components essential to the energy industry. In ANAB recognized and ISO 17025 accredited laboratories, ACE helps customers comply with OEM submissions and regulatory requirements with research and development, and independent measurement of material properties.
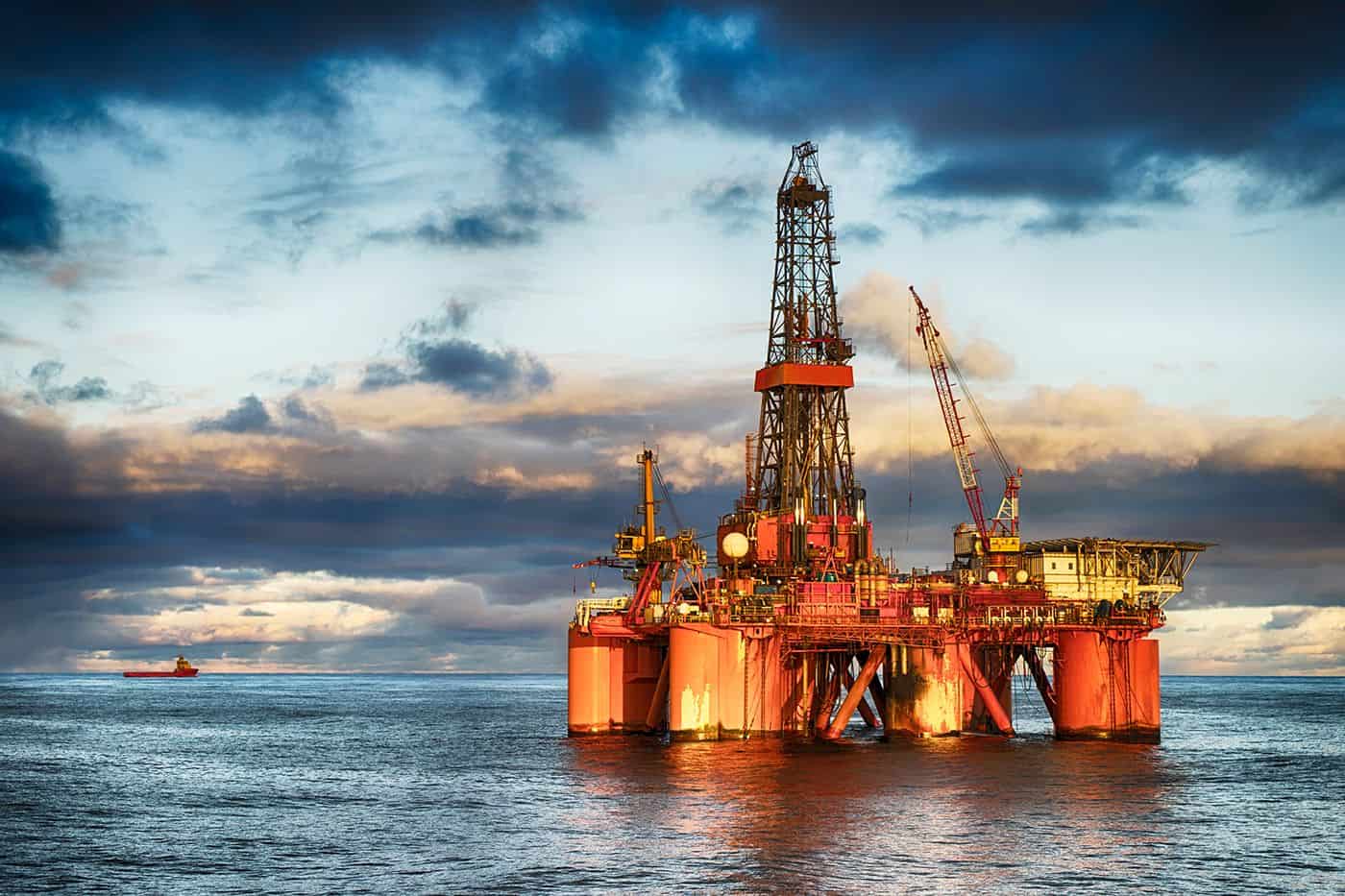
Not every hose, fitting, or seal can withstand long-term exposure to oil and gas—or other extreme variables, such as high heat, pressure, and abrasion. The energy industry relies on components that can handle a rigorous service environment and multiple intense factors at once. This often requires robust compound formulations and strategic designs to ensure long-term performance in extreme conditions.
The experts at ACE Laboratories are proud to provide comprehensive analytical testing services for oil and gas materials, products, and components. We understand the aggressive variables and conditions these components may encounter and can recreate them in a controlled laboratory environment to help you find the right material and design for every part. From new product development to performance validation to failure analysis, our team can help you make confident decisions as you bring high-performance energy products to market.
Energy Material Testing
The oil, gas, and energy industry has made incredible advancements over the years and relies on high-performance parts, components, and assemblies to execute a variety of critical functions. These components include:
- Hoses and pipes of all sizes
- Fittings
- Seals, gaskets, and o-rings
- Reservoirs
- Pumps
- Valves
- Clamps and quick connects
- Fluid transfer systems and assemblies
- Downhole drilling assemblies
The failure of a single component can lead to problems that are inconvenient at best and catastrophic at worst. For this reason, each and every component, from large hoses to tiny seals, must be tested to ensure its ability to endure extreme conditions.
Many oil, gas, and energy components are made with high-performance polymers and materials that can withstand high heat, long-term fluid exposure, and other intense variables. This often includes hydrogenated nitrile rubber (HNBR), fluoroelastomers (FKM), and perfluoroelastomers (FFKM), but a wide variety of other materials may be used. Some polymer compounds may utilize antidegradants and other ingredients to boost performance and increase resistance to extreme conditions, such as high heat and long-term fluid exposure.
Regardless of the material, comprehensive laboratory testing is an essential strategy for predicting and validating performance, while also ensuring compliance with global regulations in the energy industry.
Types of Material Testing for Energy Applications
Experienced testing engineers and laboratory technicians may use a variety of different test methods to recreate the variables of the energy industry service environment. Some of the common methods used to test oil, gas, and energy materials and components include:
- Abrasion: Depending on the application, many components, such as hoses and pipes, must perform in tight quarters and are constantly rubbing up against other parts of an assembly. Abrasion testing is designed to recreate that repeat friction and assess the material’s resistance to the effects of abrasion over a period of time.
- Dynamic Mechanical Analysis (DMA): DMA testing is a customizable method that combines multiple test parameters, including time, temperature, frequency, stress, and others, to assess the mechanical properties of a material.
- Fatigue: Fatigue testing is vital for components and materials that experience repeated loading while in service. This test method allows manufacturers to identify when their materials may start to lose their strength and stiffness—to such a degree that performance is affected—when subjected to repeated loading.
- Fluid Exposure and Aging: There are multiple different ways to test how a material will interact with fluids, such as oil, gasoline, fuel, and others, while in service. This may include long-term exposure testing or fluid aging testing, which incorporates heat.
- Pressure: Fluid transfer components of all kinds, from pipes and hoses to seals and gaskets, must be able to withstand both steady and pulsing pressures. Pressure testing recreates these forces in a controlled environment to determine whether a given component is suitable for the pressures it may face.
- Temperature: Components used in oil and gas applications often encounter extremely high temperatures while in service. Temperature testing methods can assess whether component materials can maintain their performance properties in high-heat conditions.
These methods can be combined to create a custom testing program that meets your unique needs. The experts at ACE also have years of experience conducting tests based on industry standards and OEM specifications.
Energy Materials Testing from ACE Laboratories
ACE Laboratories can help you ensure quality performance of components and materials designed for oil, gas, and energy applications. We test and certify the safety, compliance, quality, and functionality of compounds used in the energy industry.
We have first-hand knowledge of how the industry has evolved over time and the advancements happening today, so we can help you explore innovative new solutions, including clean technologies, renewable materials, sustainable alternatives to traditional energy sources, and countless others.
Our ISO 17025 accredited laboratory is equipped for analytical and physical testing services, from regulatory and OEM compliance to research and development. To learn more or discuss a project, talk to a member of our team.